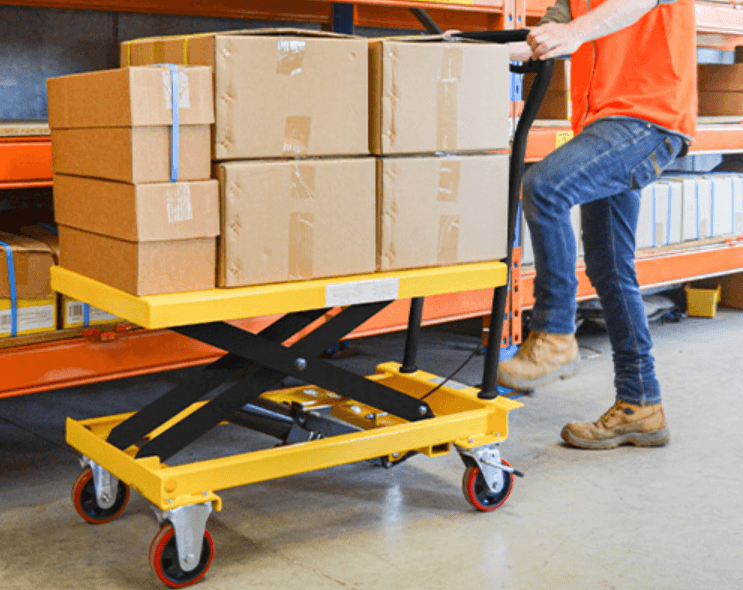
Optimizing Vertical Storage with Scissor Lifts: Elevating Efficiency in Space-Constrained Warehouses
As modern warehouses evolve to meet the increasing demands of e-commerce and rapid distribution, maximizing space has become not just a convenience, but a necessity. Floor space is finite. Ceiling height, however, offers untapped potential. The move toward vertical storage systems is transforming how facilities manage their inventory, and with this shift comes the need for safe, reliable, and efficient access to elevated areas.
Enter the scissor lift. These machines, known for their vertical stability and compact footprint, are playing a crucial role in making vertical storage viable. Through strategic use of scissor lift rental, warehouse managers can adapt their layouts, improve picking efficiency, and expand their usable storage volume—all without increasing their building’s footprint.
This article explores how space-constrained warehouses can benefit from implementing vertical storage strategies supported by scissor lifts, and how integrating this approach into everyday operations unlocks productivity and safety gains.
The Shift Toward Vertical Thinking
Warehouses are increasingly faced with a dilemma: how to store more inventory without expanding. Real estate costs, zoning regulations, and logistical limitations often make horizontal expansion either financially unrealistic or physically impossible. As a result, the concept of building upward has taken hold.
High-bay racking systems, mezzanines, multi-level shelving, and dynamic storage structures are now common solutions. However, these systems are only effective if staff can access elevated inventory quickly and safely. That’s where scissor lifts come into the picture.
Unlike ladders or scaffolding, which are often unstable or inefficient, scissor lifts provide a secure, mobile platform that can be raised or lowered as needed. They are particularly useful during racking installation, overhead maintenance, and high-position picking tasks.
See also: Grundig E-bike Technology Makes Other Bikes Look Outdated
Why Scissor Lifts Beat Traditional Access Methods
While many facilities still rely on ladders, rolling stairs, or fixed platforms, these options come with significant limitations:
- Ladders lack stability and height precision.
- Rolling stairs consume more floor space and are limited in reach.
- Fixed platforms are inflexible and can obstruct workflows.
In contrast, scissor lifts offer:
- Precise vertical access for varying storage levels
- Compact bases for tight aisle maneuvering
- Platform guardrails and emergency lowering systems
- Options for electric power, making them clean and quiet for indoor use
For warehouses operating in tight quarters, renting a scissor lift becomes a practical, non-permanent way to improve safety and access without permanently altering the facility layout.
Integrating Scissor Lift Rental Into Facility Planning
Not every warehouse needs a permanent fleet of lifts. Many operations benefit from bringing in scissor lifts only when certain projects arise:
- Installing new vertical racking systems
- Rearranging upper-level storage
- Performing inventory audits on high shelves
- Replacing overhead lighting or HVAC components
Using scissor lift rental on a project-by-project basis keeps overhead costs low and eliminates the need for permanent storage and maintenance responsibilities. Planning rental periods around facility upgrades or seasonal inventory changes allows for smarter use of capital.
Evaluating Your Warehouse for Vertical Expansion
Before implementing any vertical storage strategy, it’s essential to assess whether your facility is suitable for this approach:
- Ceiling Height: There should be sufficient vertical clearance, not just for racks but also for operator access.
- Floor Load Capacity: Both racking systems and scissor lifts require solid flooring capable of handling weight concentrations.
- Lighting and Visibility: Working at height requires clear visibility and sufficient lighting to maintain accuracy and safety.
- Aisle Width: Scissor lifts come in narrow-width configurations, but aisle spacing still matters for maneuverability.
Once these factors are understood, warehouses can begin to integrate scissor lifts into their reconfiguration plans.
Safety First: Elevating Without Risk
Whenever staff work at height, safety must be a top concern. Falls remain one of the leading causes of workplace injuries, especially in environments that use ladders or manual platforms. Scissor lifts dramatically reduce these risks by offering stable, enclosed platforms with automatic braking, emergency descent features, and non-slip surfaces.
Operators should always be trained in lift use, including:
- Recognizing lift limits and load capacity
- Using personal protective equipment when required
- Performing pre-operation safety checks
By renting newer models from trusted providers, facilities ensure compliance with the latest safety regulations and reduce the likelihood of malfunction.
Workflow Benefits of Going Vertical
Vertical storage offers more than just spatial efficiency. It can reshape how a warehouse functions:
- Faster Picking: Grouping frequently accessed items at reachable upper levels shortens retrieval times.
- Better Inventory Organization: Vertical stratification allows for clear separation of product categories.
- Improved Traffic Flow: By building up rather than out, aisles remain clearer and easier to navigate.
A well-coordinated scissor lift rental strategy ensures that workers can perform elevated tasks without interruption, particularly when accessing upper levels becomes routine.
Combining Scissor Lifts with Forklift and Boom Lift Strategies
Warehouses that rely on vertical storage often use a combination of equipment to support day-to-day operations:
- Forklift rentals move pallets to and from high rack positions.
- Boom lift rentals support infrastructure maintenance or electrical work in areas with obstructions.
- Scissor lift rentals provide safe, flat-surface access for inventory tasks, inspections, and light-duty repairs.
Creating a layered equipment strategy ensures that every aspect of your vertical plan is supported by the right tool. Rentals allow you to scale this strategy as needed without committing to long-term equipment purchases.
Considering Material Handling Equipment Compatibility
When moving to vertical systems, it’s important that all your material handling equipment works together. Forklifts used to place pallets in high racks must be compatible with aisle widths and rack design. Scissor lifts must be able to reach inventory heights and navigate through storage zones.
Facilities that plan layout changes without considering equipment dimensions and turning radii risk creating unusable storage space or damaging existing infrastructure. Coordination between warehouse design and rental planning is essential.
Budgeting for Height: Rental as a Financial Advantage
Permanent lift equipment requires upfront capital, ongoing maintenance, and operator certification programs. For warehouses with limited budgets or evolving layout plans, rental presents a practical alternative:
- Lower upfront costs
- No storage requirement during off-use periods
- Maintenance and servicing included in most agreements
- Access to newer, more efficient lift models
Renting also allows operations to evaluate what type of equipment best fits their long-term needs before making purchase decisions.
Working with the Right Rental Partner
Equipment performance is only one part of the equation. The rental partner you choose should provide reliable delivery, training resources, and knowledgeable support. Companies like Tri-Lift Industries, Inc. offer tailored guidance to help match your vertical access needs with the most appropriate scissor lift model.
Whether it’s understanding floor impact or choosing the right lift height, working with experienced providers prevents delays and improves outcomes.
Conclusion
As warehouse space becomes more valuable and more constrained, the shift toward vertical storage is not just a trend—it’s a long-term operational imperative. By leveraging scissor lift rental as a strategic asset, facilities can unlock the vertical plane, improve space utilization, and support evolving inventory demands without compromising safety or efficiency.
The path to smarter storage doesn’t always involve new construction or costly equipment purchases. Sometimes, all it takes is the right lift, at the right time, used in the right way. And for that, flexibility and planning make all the difference.